      
THE RESARO SYSTEM
gives solutions for some
of today's most
common construction problems
(press for
a quick move on the page)
RUBRIK LIST LAST DOWN ON
THE PAGE 
WHY TO USE THE RESARO
SYSTEM?
A short summary of serious problems frequently appearing at constructions
today which avoids with the RESARO system.
Computerised houses
- The construction trend of today is towards more complicated
and complex systems for heating and ventilation. It appears that
certain rooms in houses sets aside for computerised supervision
systems.
The solution
with the RESARO system
- All computer technology is possible to replace
with a uncomplicated system, that works in a simple and reliable
way, with help from natural air flows.
As an example, in the RESARO system the energy supply controls
by a simple temperature regulator placed centrally in the residence.
The Problem
Loss of energy at under floor heating
- Today's house buyers or "self-builders" wishes to
have under floor heating. The systems available on the market
are expensive, though. With reflector systems and tubes or hoses
with circulating water.
Other casts in the slab which mostly is placed directly on the
ground.
A warm concrete slab on ground causes serious energy losses downwards
the ground and casted in installations are inaccessible and must
be laid bare by motor hammer drilling at leakage.
In existing systems for under floor heating, the water temperature
has not to be below +28 degrees Celsius, when the outdoor temperature
is low, seeing that all heat is transferred via the floors to
the rooms.
A common design and by building authorities recommended modification.
COMMON DESIGN
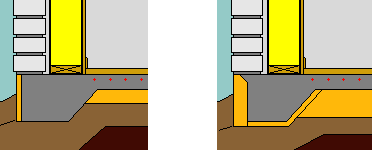 
RECOMMENDED MODIFICATION
The solution
with the RESARO system
When using the RESARO foundation design and the RESARO concrete
walls, there are no heat conductive components in contact with
the ground below, or the outdoor climate.
The load-bearing wall concrete slab is covered by a continuous
equally thick thermal insulation layer.
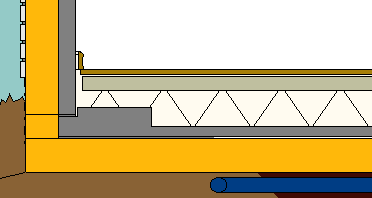
RESARO'S SOLUTION
No thermal bridges
The floor slab rests on a thermal insulation layer with a thickness
of 200 mm.
The outer walls in turn rests on the RESARO floor element. The
thermal insulation of the walls encloses the edges of the floor
element.
Therefore there are no thermal bridges.
The RESARO system:
a low temperature system
In existing systems, under floor heating signify floors with
high temperatures and hot zones.
In the RESARO system we talk about a surface temperature of +20
to +23 degrees Celsius, "Soft warmth", spreading out
over the entire area.
With RESARO elements in the bottom floor, filtered indoor air,
mixed with fresh outdoor air, circulates through the double structural
floor.
The circulated air has a temperature slightly higher than the
indoor temperature but far of the as high as in the heat coils
in conventional systems.
- This because the floor surface gets about
50% of its heat from the supply air that circulates through the
double structural floors.
The floor surface in its turn heats the rooms evenly by radiation
and convection (thermal conduction).
The other 50% stays with the supply air which gets transferred
up to the residential area, circulates behind floor skirtings
and mixes and heats the indoor air.
For this reason the supply air temperature, in the RESARO system,
can be kept considerably lower inside the elements than at conventional
under floor heating systems, where all energy is transferred
through the floor slab.
- We obtain less energy losses to the ground
in spite of the Resaro system holds warm floors in the ground
floor.
- Lower temperature on the floor surface gives
better indoor climate. Rustic wooden floors and parquet floors
are sensitive to temperatures above +25 degrees Celsius.
to rubrik list
Problems
with warm exhaust in ventilated crawl space basements in conventional
designs.
A common way to recover energy from the exhaust air is by transferring
it to the crawl space inside the foundation and from there into
a heat pump.
The foundation must have a lower pressure than the rooms to prevent
moisture from the ground to leak into the living space.
Difficulty in getting
air-tight spaces
Conventional systems don't function well, as the basement is
hard to get sufficiently tight to prevent incursion of outside
air.
The exhaust air gets sucked down into the foundation because
of the vacuum that the exhaust air fan creates.
Therefore the foundation keeps a pressure which is considerably
lower than the environment's.
Outdoor air leaks into the crawl space below the edge beams.
The result is in winter time the exhaust air is mixed in with
cold outdoor air which ruins the heat recovery.
Furthermore an exhaust air ventilated basement is a passive system,
which cannot overcome the tendency toward cold floors, with a
lower temperature than the indoor air. It is not as cold as a
slab on the ground, but not as warm as under floor heating.
Risk of condensation
in exhaust air ventilated basements:
The air temperature in an exhaust air ventilated basement is
cooler than the indoor air because the ground cools it. The exhaust
air that comes from the wet rooms of the house contains a lot
of water, that is, its relative humidity is high.
Upon warm air cooling, there is a risk for condensation. Therefore
there is a big risk for floor construction made of wood or other
organic material, which faces the ground, to be affected by rot
or mould.
The solution
with the RESARO system
- In the RESARO system heated air circulates
inside the structural bottom floor therefore damages caused by
damp is efficiently prevented.
Problems
with radon from the ground
- A slab cast directly on the ground does not provide an effective
protection from radon, even if it is very thick. In most cases
there is no protection at all, as concrete always cracks.
Up-to-date houses have, nearly always, a vacuum inside, which
is why radon gas easily finds its way up and inside the dwelling
through the cracks.
The solution
with the RESARO system
The RESARO OVER-PRESSURE FOUNDATION system
provides four effective barriers against radon infiltration.
- First barrier:
With the RESARO system solution, the radon gas dissipates under
a tarpaulin below the the bottom of the house.
When encountering ground with a high level of radon, a strong,
tightly welded tarpaulin will be used. In order to secure radon
from penetrating the dwelling, the tarpaulin is made bigger than
the foundation and reaches over the edges.
- Second barrier:
There is an over-pressure in the gravel bed above the tarpaulin
created by the exhaust air entering.
- Third barrier:
The prefabricated concrete elements are assembled on site, connected
tightly by welding and sealed by pouring cement between the slabs.
- Fourth barrier:
There is a slight over-pressure inside the circulation space
of the RESARO structural floor, which also obstructs radon from
penetrating into the house if the bottom slab cracks
to rubrik list
Problems
with moisture and mould
Construction moisture
- One of the biggest problems is so-called "sick houses"
where mould appears.
The reasons for the growth of mould are: moisture, insufficient
ventilation, improper materials, and/or poorly dried concrete
and framework, in most cases.
For example, when putty that may be made of organic material
has been used between moist concrete and the final surface coating,
chemical reactions with exhaling. Poisonous gases occur, endangering
the residents.
Mould and damage caused by dampness in outer walls behind shower
and bathtub are also common problems.
The solution
with the RESARO system
- The risk for mould formations in framework
eliminates.
When using the RESARO system the structural floors establishes
a distribution channel way for heated circulation supply air
and ventilation supply air.
Meanwhile the framework dries up.
- Even though the RESARO structural floors
do not serve as a supply air duct e.g. in department houses,
during the erecting time a simple air circulation can be arranged
inside the Resaro elements, for drying.
Possibly with help from a construction drier.
- The surface coating can be applied at an
earlier stage than with other systems.
Problems
at natural ventilated houses
Mould in framework caused by air leakage
If the house has no exhaust air fan unit which establishes a
vacuum, but just natural ventilation, a slight over pressure
will establish in top floor.
The warm and humid indoor air penetrates, at smallest openings,
through outer walls and ceiling and emits its dampness into the
thermal insulation and the wooden framework causing damage.
Places where the house
shows up damage are marked with rings
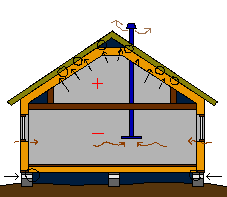

The solution
with the RESARO system
- In the RESARO system we always use an exhaust
air fan unit which establishes a slight vacuum in the house.
- RESARO AB has a patent application for the
arrangements to prevent indoor air to penetrate the thermal insulation
when using Dynamic fresh air intake.
See also the paragraph below "Dynamic fresh air intake".
Problems
with bad ventilation effect the warm seasons
In natural ventilated houses the ventilation doesn't have any
effect during the warm seasons as the qualification to create
the density divergences - hot and cold - which composes the power
for air movements, are missing.
With wet construction materials that's been stored outside, or
if it rained on the framework, maybe even on the thermal insulation,
before the roof shelter was put in place, there are great risks
for formation of mould to appear.
In a house once damaged by mould or rot, the smell and the influence
of poison remains for ever
The solution
with the RESARO system
- In the RESARO system an exhaust air fan unit
is used, therefore it is always a slight vacuum in the rooms
and the ventilation air is sufficient at all seasons.
See also the paragraph below "Dynamic fresh air intake".
to rubrik list
Problems
with mould in ducts
in hot air heating plants
- A plausible reason to the mould to appear, is inconvenient
placements of ducts for air heating inside the thermal insulation
in the ceiling.
The ducts must be placed above the roof trusses lower chords,
which means, closest to the in wintertime cold outdoor air.
The heat from the ducts rises and gives off its energy
to the outdoor air.
A plausible reason why
these houses requires a lot of energy!
The ducts goes through cold parts of the attic.
Warm indoor air which contains a considerable amount of humidity,
passes through the ducts and cools of.
To this, the risk for the temperature to get below the dew point
is serious, causing moisture on the duct partitions.
If there at the same time is dust to be found in the ducts the
possibilities for mould to appear.
The solution
with the RESARO system
- The risk for mould to appear in air ducts
is completely eliminated.
The simple solution
with the RESARO system is to always feed the heated supply air
from beneath, always in warm spaces and always indoors.
Problems
with mould/mildew behind kitchen cupboards
- A place where mould often appears is behind kitchen cupboards
at outer walls. This because the cupboards mostly are crammed
with kitchen utensils and food articles which works as an thermal
insulation.
Bad ventilation behind the kitchen cupboards and a cold floor,
e.g. a slab cast directly on the ground, or a floor on top of
a fresh air ventilated crawl-space basement, creates the necessary
conditions for mould.
Moisture, nourishment and oxygen,
The solution
with the RESARO system
- When using the RESARO system the heated ventilation
air is lead behind the kitchen cupboards at the outer walls.
The supply air passes behind the cupboards, through the cupboard
recesses for the skirtings and then into the room.
Mostly it also passes the dishwasher.
Problems
with mould inside an outer wall in a shower
- With consideration of space, a shower is often placed next
to an outer wall. Even though a very thick membrane isolation
is placed behind the surface coating inside the shower, moisture
always penetrates the membrane because of vapour pressures.
Cold surfaces always attract moisture.
There is always a risk for mould to appear.
The moisture accumulation increases the risk of wallboards to
swell and then break the glazed tiles.
The solution
with the RESARO system
- A cavity behind the wallboard in the outer
wall for circulated indoor air, guided out on a level with the
ceiling of the wet premise, makes an efficient stop for the moisture
moving towards the cold outer wall.
The RESARO system gives
an opportunity to place a shower next to an outer wall without
the risk of condensation inside the wall.
to rubrik list
Dynamic
fresh air intake
Problems
with existing systems using dynamic insulation technique for
ventilation.
(The design of the RESARO system is designated "Dynamic
fresh air intake")
Problems
with two-storey houses with dynamic insulation.
In winter time in two-storied houses the warm indoor air creates
an over pressure in the higher parts of the house, because of
diversities of the density (warm air is lighter than cool).
Therefore the indoor air makes its way upwards.
(Compare natural ventilation with self
density draught)
The solution
with the RESARO system in two-storied houses:
- In the RESARO system the roof is furnished
with an additional ceiling inside the roof's thermal insulation,
creating a compartment between the insulation and the additional
ceiling boards.
- A vapour retarder placed above the ceiling
boards prevents the indoor air from getting to the insulation,
and cause damage.
A patent approved construction gives an even distribution of
the inlet air over the entire insulation area.
A collection box transfers the fresh outdoor air into the indoor
circulation system . This arrangement makes sure that humid indoor
air will not go the "wrong way" out towards the thermal
insulation.
- Trough the above procedure to let the circulation
air transfer the ventilation air into the rooms it also avoids
indoor air to get in contact with cool insulation.
Problems
Complicated solutions for circulating hot air heating systems
at 1 1/2- storied- and two-storied houses
- The conventional hot air heating systems, in a 1 1/2-floors-
or a two-storied house, are very complicated with many ducts.
Distribution ducts, for heating and ventilation of ground floor
and supply ducts which leads up to and are installed inside the
roof's thermal insulation for the ventilation of the top floor,
are often placed below the intermediate floor in horizontal steel
ducts which then changes direction, going upwards.
Covered by immersed ceilings, inside the rooms.
Work operations: The ducts shall be hanged, covered by wood battens
and gypsum boards. There after puttying and painting.
This is an expensive installation and difficult to maintain.
The solution
with the RESARO system
- With the RESARO system the heat and ventilation
air is supplied through the structural floors which are slightly
over pressured.
The air flows slowly up behind the floor skirtings along the
outer walls and further to a centrally placed return duct leading
to for a heat unit for tempering and filtering.
Fresh outdoor air is added in the return duct.
Problems
with ventilating of top floor
- A conventional way to guide air to top floor is to use air
ducts going trough air inlets (=holes) in the floor or in the
wall.
Because of technical reasons a concentrated inflow appears which
gives a bad conversion of ventilation air.
An other procedure is to use a hollowed skirting to distribute
the supply air along a wall into a room.
But hollowed skirtings are expensive, often appears unattractive
and obstructs furnishing.
The solution
with the RESARO system
- Using the RESARO system you can ventilate
the top floor with the same system as for the ground floor.
- The Resaro system shows a completely new
way to transfer supply air, along the skirtings, into a top floor
gable room.
This obtains trough a cavity placed in the first floors end wall
(or a wall near by). This cavity links the circulation space
inside the bottom structural floor with the gable room.
- This procedure gives a rich inlet, which
gives an effective conversion of the ventilation air in the entire
room.
- We get the advantage of rooms without radiators
and unattractive hollowed skirtings and convenient to furnish
and clean.
to rubrik list
Problems
with heat exchangers for heat recovery.
- A not so known problem with heat exchangers, is that they must
be cleaned at least once a year.
When warm humid exhaust air coming from wet premises meet the
heat exchangers cold surfaces, chilled by winter tempered outdoor
air, condensation always appears.
When dust in the exhaust air, the necessary conditions for mould
creates in the exchanger and mould spores accompanies the
outdoor air into the rooms.
This can be one of
the reasons why people develop allergies.
The solution:
The RESARO-system without a recovering unit
- Using the complete solution of the RESARO
system in a standard insulated house, there are no recovery units
needed to settle the demands of the building codes.
In a standard insulated
house with......
- lower indoor temperature thanks to warm floors
- energy recovery with the design for fresh
air intake through the roofs thermal insulation where the heat
is transferred back into the house
- the arrangement with the "over pressure
foundation" where the bottom parts of the house heats by
the exhaust air.....
........there is no
need for a heat recovery unit.
- At cold seasons the intake of fresh outdoor
air goes through the roofs thermal insulation and leads the warm
air back in again, therefore the insulation can be made a lot
thinner than at a conventional application, without losing its
effect.
- The fact is that the thickness of the roofs
insulation is settled regarding the needs to provide the house
from heat from above, at warm seasons.
Problems
No profits from using an exhaust air heat pump
- Exhaust air heat pumps are expensive to buy and to install
It has turned out that the lifetime of its vital parts is no
longer than about 8 years, why service costs usually comes up
to a higher sum than the savings.
The
solution
with the RESARO system
- When using the complete RESARO system solution
there is no need for heat recovery units for a standard insulated
house.
- However the RESARO system works excellent
together with an exhaust air heat pump.
But with today's energy costs the costs for purchase and installation
of an exhaust air heat pump "don't pay back" with this
system.
- When higher energy costs the RESARO system
would be excellent to complete with an exhaust air heat pump.
Therefore our installations today always are prepared for a future
connection with an exhaust air heat pump.
to rubrik list
This text contains following
titles
WHY USE THE RESARO SYSTEM?
Complications in today's construction
Computerised houses
Loss of energy and problems when using a slab cast on ground
for under floor heating
Problems when using exhaust air in ventilated crawl space in
conventional foundations
The risk for condensation promoting mould
Ambient radon
Problems caused by moisture and mould
Problems at natural ventilated houses
Mould in framework caused by air permeates
Insufficient ventilation capacity at warm seasons
Mould in ducts at air heating plants
Mould behind kitchen cupboards
Mould in bathroom's outer walls
Dynamic fresh air intake
Problems with common dynamic ventilation systems in two-storied
houses
Complicated solutions for circulating hot air heating systems
at 1 1/2- storied- and two-storied houses
Problems at second floor ventilation
Problems with heat exchangers for heat recovery
No profits from using an exhaust air heat pump
TEXT APPENDIXES
Information about the RESARO system for small houses
Short information about the
"Dynamic fresh air intake"
to THE RESARO SYSTEM PAGE
to THE RESARO TECHNOLOGY PAGE
to THE RESARO HOME PAGE
     
|